Support for HAPPY 7-Needle Journey
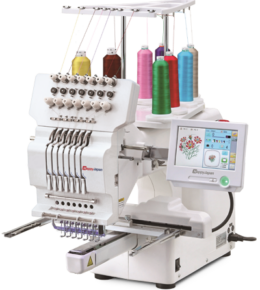


On this page, you’ll find support information for the HAPPY HCH-701 7-needle Journey 1-head embroidery machine.
SUPPORT TOPICS
ASSEMBLY & SETUP
Machine Assembly and Setup: Follow THIS LINK for instructions on assembly and setup for this machine.
TROUBLESHOOTING YOUR MACHINE
Troubleshooting for New Operators: Follow THIS LINK for a basic troubleshooting guide for this machine.
FIRMWARE
Information and Downloads: Follow THIS LINK for information about firmware updates for this machine.
ERROR CODES
Common Error Codes: Follow THIS LINK for information about common error codes, including explanation and possible remedies, for this machine.
LINKS & DOWNLOADS
Useful Links and Downloads: Follow THIS LINK to view common links and downloads for this machine.